Introduction
Process costing is a vital aspect of cost accounting, enabling businesses to allocate costs accurately and make informed decisions. However, mastering process costing can be challenging, and even small mistakes can lead to significant errors in financial data. In this blog post, we’ll delve into five common mistakes in process costing, drawing insights from the expertise of Parag Gupta, a renowned authority in the field of accounting and finance.
Want to understand more about Process Costing in depth, read this.
5 mistakes to avoid in Process Costing at CA Inter level are:
- Neglecting Detailed Documentation: One of the most common mistakes in process costing is neglecting detailed documentation. Parag Gupta emphasizes the importance of meticulous record-keeping to track every cost incurred during the production process. Without accurate documentation, it becomes challenging to allocate costs correctly, leading to distorted financial reports and flawed decision-making.
- Overlooking Variable Costs: Another mistake to avoid is overlooking variable costs. Parag Gupta highlights the significance of identifying and properly accounting for variable costs associated with each production process. Failure to do so can skew cost calculations and hinder the ability to determine the true profitability of products or services.
- Ignoring Process Variability: Process variability is a crucial factor that should not be ignored in process costing. Parag Gupta emphasizes the need to account for variations in production processes, as these can impact cost allocation methods and overall accuracy. By acknowledging and addressing process variability, businesses can refine their costing techniques and improve decision-making.
- Misinterpreting Overhead Allocation: Incorrect overhead allocation is a common pitfall in process costing. Parag Gupta warns against misinterpreting overhead costs and emphasizes the importance of using appropriate allocation methods. Failure to allocate overhead costs accurately can result in distorted product costs and misleading profitability analysis.
- Failing to Regularly Review Processes: Lastly, failing to regularly review and update process costing methods is a mistake that businesses should avoid. Parag Gupta advocates for continuous improvement in costing practices to adapt to changing business dynamics and market conditions. By regularly reviewing processes, businesses can identify inefficiencies, optimize cost allocation, and enhance overall performance.
5 tips to avoid mistakes in Process Costing by Parag Gupta sir:
Tips | Description |
---|---|
1. Detailed Documentation | Maintain thorough records of production costs incurred at each stage to ensure accurate cost allocations and financial reporting. |
2. Consider Variable Costs | Identify and account for fluctuating costs associated with production processes to avoid skewed cost calculations and inaccurate profitability assessments. |
3. Address Process Variability | Recognize variations in production processes and adjust cost allocation methods accordingly to ensure accurate cost estimations. |
4. Accurate Overhead Allocation | Allocate overhead costs correctly to prevent distorted product costs and ensure reliable profitability analysis. |
5. Regular Process Review | Periodically review and update process costing methods to adapt to changing business dynamics and optimize cost allocation for improved performance. |
These tips provide actionable advice to help businesses avoid common mistakes and enhance the accuracy of process costing.
Also read CA Inter Costing suggested answers by CA Parag Gupta of May 24 on Process Costing
Conclusion
Process costing is a critical tool for businesses to determine product costs and make informed decisions. By avoiding these five mistakes outlined by Parag Gupta, organizations can enhance the accuracy of their process costing data and improve overall financial performance. Remember to prioritize detailed documentation, account for variable costs, address process variability, allocate overhead costs accurately, and regularly review and refine costing processes for optimal results.
FAQ’S
The five steps in process costing are to analyze inventory, convert incomplete units to completed units equivalent, determine total expenses, calculate cost per unit of output, and allocate costs to completed and incomplete units.
The four steps necessary to complete a cost of production report in a process cost system are:
Allocate costs to transferred and partially completed units.
Determine the units to be assigned costs.
Determine the cost per equivalent unit.
Calculate equivalent units of production.
Process costing provides valuable insights into the costs of producing similar products on a large scale. It helps companies optimize their operations, improve efficiency, and maintain a competitive edge in the market.
Process loss is defined as the loss of material arising during the course of a processing operation and is equal to the difference between the input quantity of the material and its output. There are two types of material losses viz. ii) Abnormal loss. (i) Normal Process Loss: It is also known as normal wastage.
Want to ENROll to our classes?
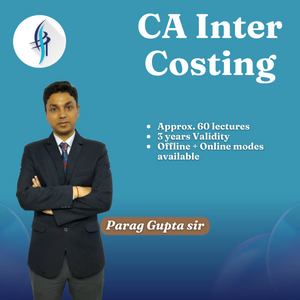
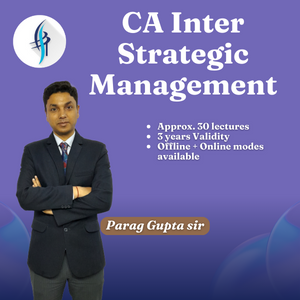